Asset Integrity Management (AIM) refers to the discipline that aims to ensure industrial assets perform their functions accurately and efficiently throughout their lifecycle, all while maintaining safety and sustainability. In this context, a robust and effective asset integrity management program spans every stage, from asset design to decommissioning, aiming to mitigate risks to the environment, people on the field, and the industrial installation of which they are a part.
This blog explores the major challenges of Asset Integrity Management and how the Oil and Gas industry is facing the digitalization of this important discipline.
Signs of unoptimized asset integrity management
Managing industrial assets integrity is a major necessity within industrial plants, especially in complex-process environments such as oil and gas, mining, and refinery plants. These industries operate under high complexity, where detecting minor failures often requires extensive labor and is not always accurate.
1- Inefficient budget allocation
Imagine a large industrial plant where minor failures go unnoticed, and maintenance plans fail to address them adequately due to process bottlenecks or poor prioritization. Maintenance teams usually operate with a fixed budget, but struggle to allocate it effectively. This inefficiency is not due to a lack of funds but rather a lack of accurate and timely information about asset conditions and failure risks. Without reliable data, decisions may prioritize the wrong assets, delay necessary interventions, or underestimate the cost of potential failures, ultimately leading to higher long-term expenses and operational risks.
2- Delayed diagnosis
In industrial plants, the time it takes to identify the integrity status of an asset and detect anomalies can often be excessively long. When diagnosing a problem is slow, and the time required to implement corrective actions is even greater, minor issues can evolve into significant risks before they are addressed. This delay in the identification-to-solution cycle creates vulnerabilities within the operation, exposing the plant to higher safety hazards, unplanned downtime, and elevated maintenance costs.
3- Unplanned downtime
When assets begin to fail frequently, minor disruptions escalate within the plant, leading to unplanned production downtime. As these issues compound, employees face increasing risks, and the likelihood of a large-scale failure looms closer. This is precisely the kind of scenario every operation strives to avoid—one that effective Asset Integrity Management is designed to prevent.
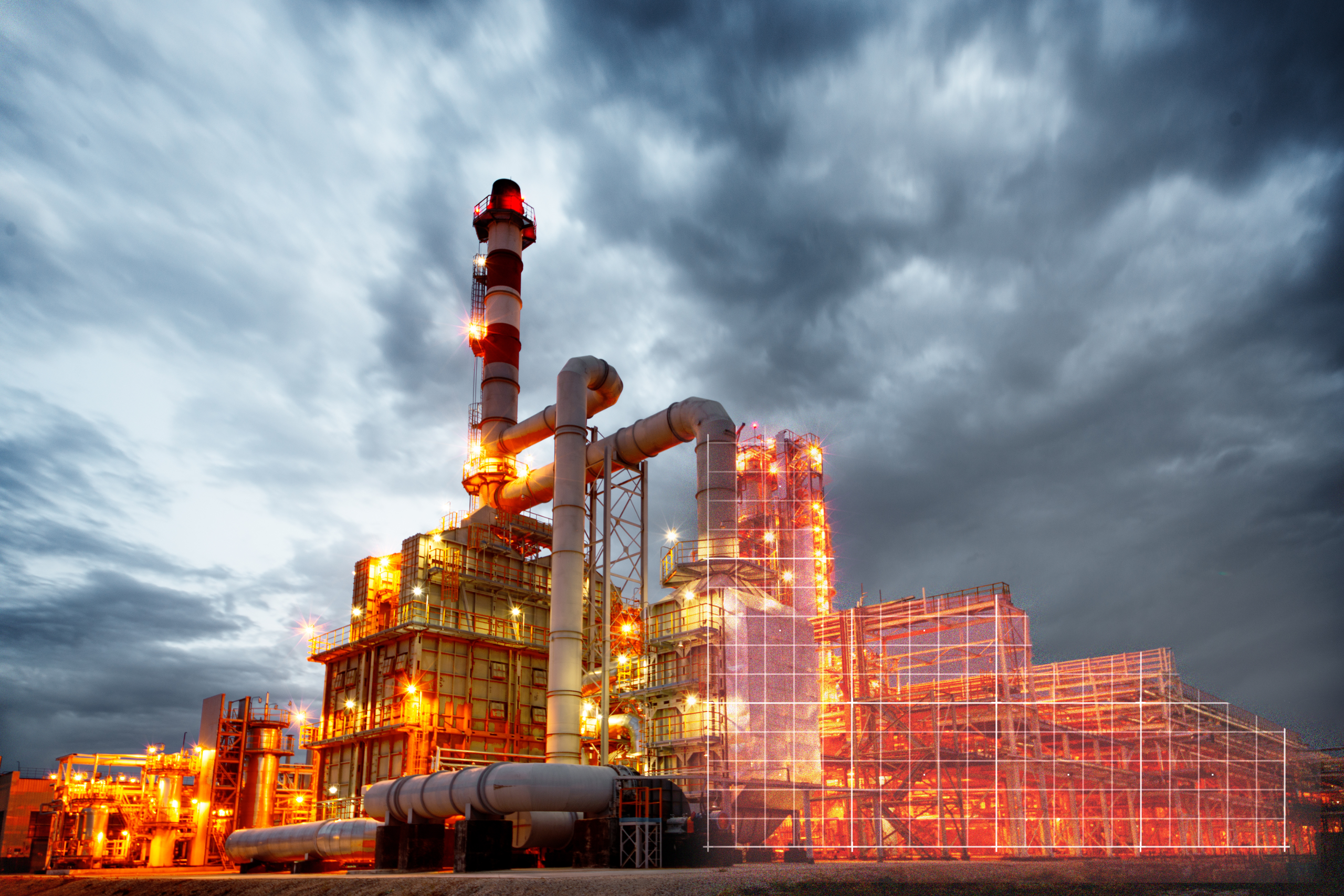
These are early signs of unoptimized integrity management. In this context, a solid AIM program requires the support of real-time data collection and algorithmic diagnostics to ensure resources are allocated effectively and to prevent avoidable maintenance costs. Thus, if industrial operations want to optimize how their assets’ integrity is managed, they will have to shift their AIM approach to a digitized one. However, AIM being such an important discipline to operational efficiency, why do industries still struggle to manage it efficiently?
Why Industrial Operations Struggle to Manage Asset Integrity
One of the biggest challenges in the industry is balancing performance, risk, and costs. The harmony between these three factors will reflect in an optimized management of investment, time, and resources allocated so that the longevity of the components of a system is preserved. However, intricate process complexities, aging infrastructure, and evolving regulatory requirements tend to disrupt this balance.
For this purpose, inspection teams play a critical role in determining whether assets are functioning as expected without exhibiting wear, cracks, or corrosion that could lead to unplanned downtime. Achieving this requires tools capable of accurately monitoring and tracking asset effectiveness. Yet, reliance on traditional inspection methods often limits visibility into real-time asset conditions, increasing the likelihood of failures going unnoticed.
Another challenge is the integration of disparate data sources. Industrial plants often rely on multiple systems to collect and store asset data, but without proper integration, this information can become siloed, delaying decision-making and reducing operational efficiency. According to The Journal of Petroleum Technology, 80% of employee time in the offshore industry is spent looking through unstructured data to inform decisions. Additionally, as global operations expand, managing a consistent approach to AIM across geographically dispersed sites becomes increasingly difficult.
Equally important is ensuring maximum safety within industrial facilities. Effective maintenance and inspection processes must identify failure mechanisms and address their root causes. This comprehensive approach guarantees the optimal lifespan of assets, minimizes downtime, and ensures consistent production output. To achieve this, organizations must invest in advanced tools and foster a culture of proactive maintenance, where predictive insights are leveraged to anticipate and mitigate potential risks.
The adequacy of the above processes will guarantee the optimal lifetime of assets within the installation, resulting in the continuity of an extraction and production line with the minimum possible downtime and lost performance.
Leveraging enhanced asset integrity management in Oil and Gas industries
Overcoming these challenges demands a shift from traditional methods to advanced, technology-driven solutions. This digital age presents both opportunities and challenges for AIM. Advanced technologies like Digital Twins, Artificial Intelligence (AI), and Data Analytics are revolutionizing how asset integrity is managed. These innovations enable real-time monitoring, predictive maintenance, and enhanced risk assessment, improving asset performance and minimizing downtime.
Indeed, digitalization offers transformative solutions to address the inefficiencies commonly associated with unoptimized Asset Integrity Management. For example, the challenge of inefficient budget allocation can be mitigated through the integration of advanced data analytics and AI-driven platforms. These tools aggregate and analyze data from facility imaging, historical performance records, and real-time asset conditions, enabling maintenance teams to prioritize investments where they are needed most. By accurately predicting the likelihood of failures and the potential impact of neglecting specific assets, organizations can allocate budgets more effectively. This shift ensures resources are directed toward high-risk areas, avoiding unnecessary expenses and reducing long-term operational risks.
Besides that, the problem of delayed diagnosis is tackled head-on by leveraging technologies like real-time condition monitoring and predictive maintenance. The combination of Reality Capture and machine learning algorithms allows operations to continuously monitor the health of assets and detect anomalies before they escalate into major issues. These technologies significantly shorten the time between identifying an issue and implementing corrective action. For instance, AI-driven systems can flag early signs of wear or corrosion, prompting timely interventions. This proactive approach minimizes the risk of small problems evolving into catastrophic failures, enhancing both safety and operational continuity.
Finally, unplanned downtime, a critical issue for industrial operations, is also addressed through digitalization. Predictive analytics tools –supported by AI– help foresee potential disruptions by analyzing patterns and trends in equipment performance. These tools enable maintenance to be scheduled based on actual asset conditions rather than reactive responses to failures. Additionally, Digital Twins—virtual replicas of physical assets—allow operators to simulate scenarios, predict the outcomes of maintenance decisions, and optimize workflows. This level of insight ensures that maintenance activities are performed efficiently, reducing the frequency and duration of downtime while maintaining consistent production levels.
In an interview with Forbes magazine, Dean Arnison, global product leader-subsea of production systems, and services at BHGE, explains how companies in the Oil and Gas sector are embarking on this digital journey. According to Arnison, industries are looking for increased productivity and reduced costs, with new business models, strong partnerships, and integrated service models. Arnison believes that most oil and gas companies are on a similar journey, looking at how to reduce basic costs while exploring ways in which digital can be leveraged to optimize asset production through a better understanding of failure and inefficiencies.
Conclusion
The implementation of Asset Integrity Management (AIM) systems has become an indispensable requirement for industries striving to maintain seamless production operations while achieving optimal productivity, complying with regulations, and ensuring the utmost safety for their structures and personnel. For this purpose, Vidya Technology developed a software platform with AI-driven Asset Integrity Management to help industries achieve higher productivity levels and capitalize on their assets’ full potential while operating with ease. As a result, the solution allows for data-driven decision-making, enabling timely interventions, resource optimization, and improved asset performance.