Digital twin technology has attracted increasing attention in the industry due to the great benefits generated by its implementation.
A digital twin consists of a technology capable of mirroring a physical object in the virtual sphere so that a constant flow of data is established between the parties. Although the concept is widespread, a true digital twin is capable of performing actions from the physical as well as the virtual sphere.
Other concepts such as Digital Shadow and Digital Model can also be easily confused with a true digital twin, however, these concepts do not have the same level of connectivity that a digital twin has.
Digital Twin for Maintenance and Operation Phase
The model proposed by Michael Grieves has as a fundamental characteristic the interoperability in all phases of the asset lifecycle (PLM), nevertheless it is worth highlighting the application of this technology specifically for the operation and maintenance phase.
In complex industries, such as process industries, for example, the responsible for integrity management (the discipline in charge of maintenance and inspection of assets) has many challenges.
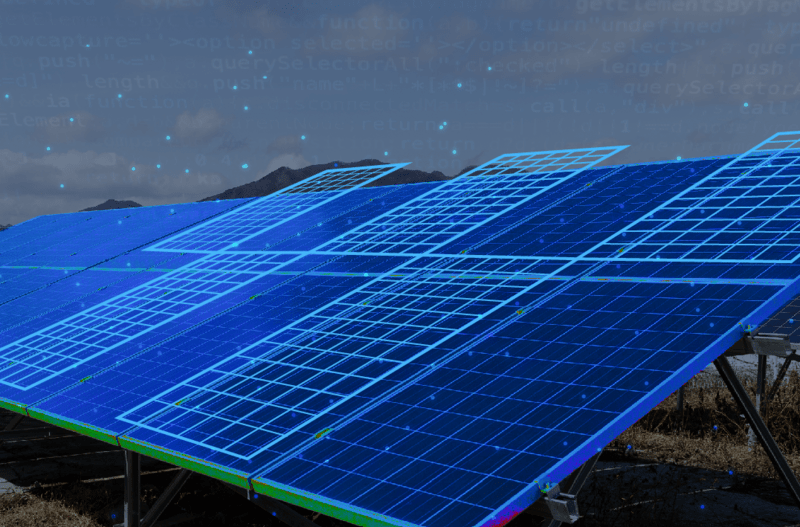
solar panel digital twin
As these industries have a large number of assets, the person in charge must organize maintenance and inspection rounds, and the operators have to dig through different systems in an effort to find manuals and procedures to perform the task.
Normally, these industries have a strict budget for the execution of these activities, that is, if some unforeseen failure occurs, the person in charge must solve the problem based on his available resources.
The execution flow of maintenance and inspection activities in this scenario opens gaps for the disorganization of information among teams, systems, and decision-makers. Therein lies the opportunity generated by the Digital Twin technology.
Applied in the maintenance and operation phase, an authentic digital twin is able to centralize all information regarding the workflow of asset integrity management programs in a single system. Obtaining all the necessary information for the execution of inspection and maintenance journeys, besides making the activity more assertive, requires less effort and time from the workforce.
Beyond, by virtue of the interoperability of the tool, the digital twin can visually favor the allocation of resources. Because of the continuous data flow, it is possible to establish areas of higher risk, and stagger activities among operators for inspection.
These, in turn, can automatically synchronize information gathered in the field to synchronize the model.
Finally, the technology can be equipped with Artificial Intelligence algorithms that, besides processing and contextualizing the extracted data, can be capable of generating outputs such as the budget needed to execute maintenance and inspection activities, estimated time of asset degradation, besides simulations of specific scenarios for the operation.
Certainly, the industrial sector has much to gain with the implementation of this technology in its processes and operations. Specifically, in the operation and maintenance phases, the use of a digital twin can mean less risk, greater efficiency and productivity of teams, total control over the operation, and greater profitability.
If you want to understand more about the technology and how it can optimize the maintenance and inspection journeys of the industry, please access this link.