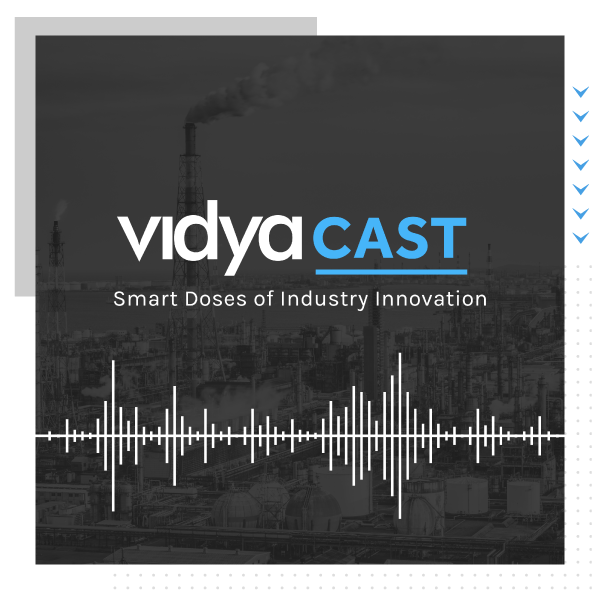
Smart doses of Industry Innovation
Latest Episode
All Episodes
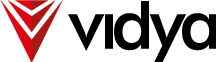
Our Technology is Attested by the Industrie’s Leading Companies
Our innovative solutions have enabled Vidya to partner with large companies
Our company is trusted by:
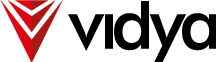
Smart doses of Industry Innovation