Introduction
Asset integrity management (AIM) is the process of ensuring that assets are maintained in a safe and reliable condition throughout their life cycle. This is especially important for offshore facilities, which are subject to unique harsh environmental conditions and complex operating environments. The traditional way of ensuring integrity is based on paper and visual inspections. Taking into account that technology is becoming more present within Oil and Gas operations, the application of state-of-the-art technology is fundamental to enhance the overall process of asset integrity management.
How its currently done
The current process of AIM is largely manual and relies on a variety of physical inspections and data collection methods.
One of the main bottlenecks generated by manual methods of inspection and maintenance is the high cost and risk associated with sending personnel to offshore facilities. These units are often located in remote and hazardous environments, which makes it difficult and expensive to access them. Additionally, manual inspections can be time-consuming and error-prone.
Another bottleneck is the lack of real-time data on the condition of assets. Manual inspections typically only provide a snapshot of the asset’s condition at the time of the inspection. This can make it difficult to identify and address potential problems before they lead to failures.
In addition to these challenges, manual methods of AIM can also lead to a number of other challenges, such as:
- Inefficient maintenance planning: Without real-time data on the condition of assets, it can be difficult to prioritize maintenance tasks and develop effective maintenance plans that don’t overlap the workforce.
- Unplanned downtime: Manual inspections and maintenance can fail at some point and if so, lead to unplanned downtime, which can be a nightmare to the production systems involved.
- Reduced safety: Manual inspections and maintenance can expose operators to climbing or hard-to-reach areas, turning the risk involved in the activity higher than expected.
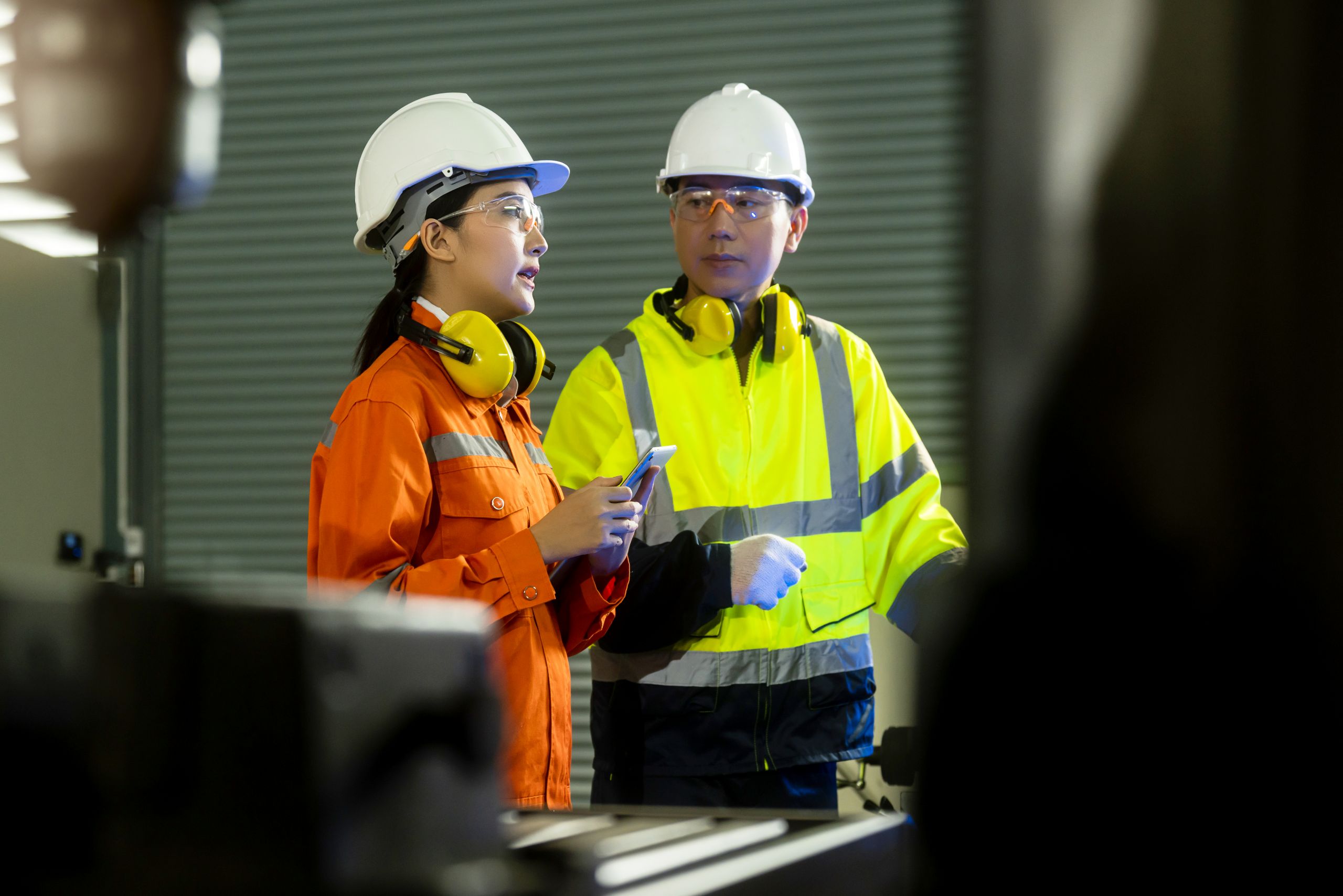
engineer cooperation Two asian maintenance engineers men and women inspect relay protection system with tablet device to control quality control process work a heavy industry manufacturing factory
New Opportunities to Asset Integrity Management
Emerging technologies and concepts, such as artificial intelligence (AI), asset performance management (APM), and analytics, are beginning to be applied to the operation and maintain of Oil and Gas operating units, addressing and providing new perspectives to the challenges of manual asset integrity management.
Even though technologies are more mature in different areas of operation, the opportunities leveraged to the asset management discipline are astonishing.
These technologies can help to automate tasks, improve data collection and analysis, and develop more effective maintenance strategies. By embracing these new approaches, offshore companies can improve the efficiency, effectiveness, and safety of their production facilities.
Some of the direct improvements of using these techniques are:
- Remote monitoring: AI and APM can be used to monitor the condition of assets remotely. Enabling companies to reduce the need for people on board.
- Predictive maintenance: Algorithms can be used to develop predictive maintenance models for offshore assets. This can help companies to prioritize maintenance tasks and avoid unplanned downtime.
- Risk assessment: Analytics tools can be used to analyze data from assets and contextualize them to risk documents and other sources to identify and categorize risks to asset integrity.
Conclusion
By embracing technology, offshore companies can generate enhanced safety, HSE, and better production outcomes.
These technologies can assist companies in enabling enhanced asset integrity management create independence for a historically manual execution model and turn it into a total digitalized process with accurate insights, enhanced costs, and most importantly; Better safety for professionals in the field.